what is a concrete block making machine
Fév 28, 2025
A concrete block making machine is a specialized device used to manufacture concrete blocks, bricks, pavers, and other construction materials by compacting a mixture of cement, aggregates (sand, gravel), and water into molds. These machines are essential in construction for producing uniform, high-quality blocks efficiently. Here’s a detailed breakdown:
How It Works:
- Mixing: Raw materials are blended (either manually or via an integrated mixer) to form a semi-dry concrete mix.
- Molding: The mix is fed into molds, where hydraulic or mechanical pressure compresses it. Vibration is often applied to remove air pockets, ensuring density and strength.
- Demolding: The freshly formed blocks are ejected from the molds.
- Curing: Blocks are left to dry and harden, either naturally (air-cured) or in controlled environments (steam-cured chambers for faster results).
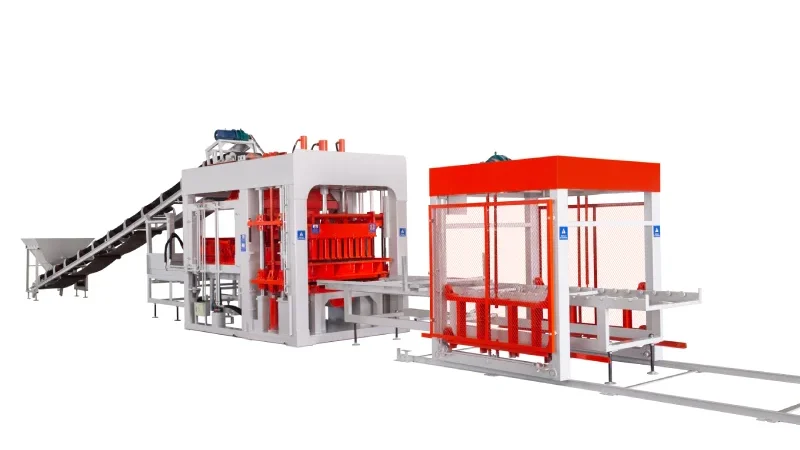
Key Components:
- Hopper: Holds raw materials before mixing.
- Mixer: Combines cement, aggregates, and water (optional in some models).
- Mold System: Interchangeable molds for creating different block shapes (hollow, solid, paving, interlocking).
- Compaction System: Uses vibration, hydraulic pressure, or mechanical force to densify the mix.
- Control Panel: Manages automation levels (manual, semi-auto, or fully automatic).
- Conveyor System: Transports blocks for stacking or curing (in advanced models).
Types of block making Machines:
- Manual/Semi-Automatic:
- Operated via levers or pedals; low output (100–500 blocks/hour).
- Affordable, suitable for small businesses or rural areas.
- Fully Automatic:
- High-capacity (1,000–5,000+ blocks/hour) with minimal human intervention.
- Integrated mixing, molding, and stacking systems; ideal for large-scale production.
- Mobile Machines:
- Portable units for on-site block production, reducing transport costs.
- Stationary Plants:
- Fixed installations for continuous, high-volume output.
Applications:
- Building construction (walls, foundations).
- Pavement and landscaping (pavers, curbstones).
- Specialty blocks (insulated, decorative, interlocking for erosion control).
Avantages:
- Efficiency: Faster production than manual methods.
- Consistency: Uniform block size and strength.
- Cost-Effective: Reduces labor and material waste.
- Versatility: Adaptable to different block designs via mold changes.
Considerations:
- Initial Investment: Higher cost for automated systems.
- Power Source: Electric, diesel, or hybrid options.
- Maintenance: Regular cleaning of molds, checking hydraulic systems.
- Local Standards: Machines must comply with regional construction codes (e.g., ASTM, IS, EN).
Environmental Impact:
- Can incorporate recycled materials (crushed concrete, fly ash).
- Optimizes resource use, reducing waste.